TOP > Technology > Precision Casting Technology Using Rapid Ceramic Molding Method |
Precision Casting Technology Using Rapid Ceramic Molding Method |
We produce molds for precision castings by our original method
called "Rapid Ceramic Molding Method".
Conventional method requires 5 to 6 days to make the molds whereas our
method can provide them in a few hours because drying process is unnecessary. |
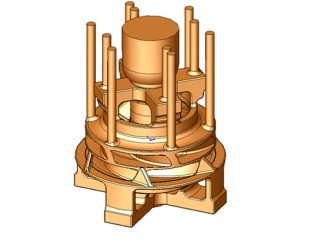 |
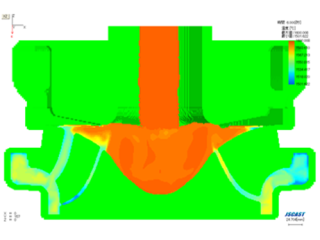 |
■Casting Design by Utilizing Simulation Software |
3D model data and casting plans are designed based on drawings
and CAD data from customers. Fluidity and solidification of molten metal
are checked by casting-simulation software and are fed back to casting
plan. |
■Printing Solid Models from 3D Data |
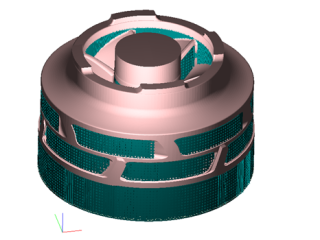 |
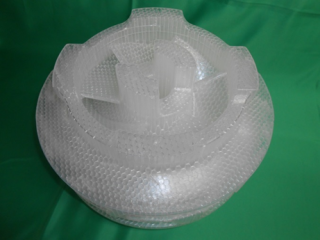 |
Solid models are printed from 3D data (STL). By stereolithography
method, UV curable resin is hardened by laser. The maximum model size is
400 × 400 × 300 mm. Customers can check the appearance at this stage. |
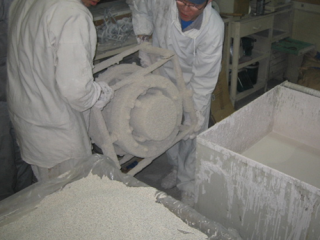 |
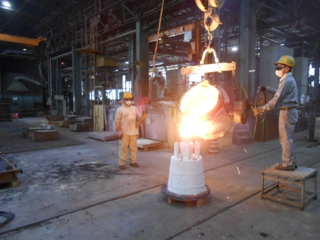 |
■Castings |
The solid models made by stereolithography can be used as lost
patterns to make ceramic molds. The molds are made by coating the solid
models with ceramic powder repeatedly until the ceramic layers are made.
Then the models are put into a furnace of 1000℃ to be burned to ashes and
the ceramic molds remain. Finally by pouring melted metal into the molds,
we can take out castings. Casting surfaces are very smooth, and products
of complex shapes can be created in very short time. |
■Types of Material |
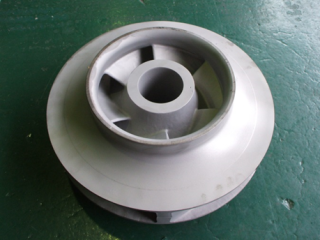 |
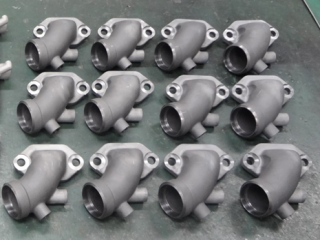 |
Materials for castings are cast iron, stainless steel, aluminum
and bronze. Any number of products even one item can be manufactured depending
on customer's requests. |
|
Go back to top of this page |
|
Copyright (C) 1998 Imanishi Manufacturing Co.,Ltd. All Rights Reserved. |
|